The Definitive Guide for Alcast Company
The Definitive Guide for Alcast Company
Blog Article
The Greatest Guide To Alcast Company
Table of ContentsAlcast Company Fundamentals ExplainedGetting The Alcast Company To WorkGet This Report about Alcast CompanyNot known Facts About Alcast CompanyNot known Incorrect Statements About Alcast Company Not known Details About Alcast Company
The refined distinction exists in the chemical content. Chemical Contrast of Cast Aluminum Alloys Silicon advertises castability by decreasing the alloy's melting temperature and boosting fluidity throughout spreading. It plays a crucial duty in permitting elaborate mold and mildews to be loaded accurately. Furthermore, silicon adds to the alloy's toughness and put on resistance, making it valuable in applications where durability is critical, such as vehicle components and engine components.It likewise boosts the machinability of the alloy, making it simpler to process into finished items. By doing this, iron adds to the overall workability of light weight aluminum alloys. Copper enhances electrical conductivity, making it helpful in electrical applications. It additionally boosts rust resistance and adds to the alloy's general toughness.
Manganese contributes to the strength of aluminum alloys and enhances workability (Aluminum Casting). It is generally made use of in wrought light weight aluminum items like sheets, extrusions, and profiles. The existence of manganese help in the alloy's formability and resistance to fracturing throughout manufacture procedures. Magnesium is a light-weight aspect that provides strength and influence resistance to aluminum alloys.
Our Alcast Company Ideas
It enables the production of light-weight parts with exceptional mechanical buildings. Zinc boosts the castability of aluminum alloys and helps manage the solidification procedure during casting. It boosts the alloy's strength and firmness. It is commonly discovered in applications where elaborate shapes and fine details are essential, such as ornamental spreadings and certain auto parts.

The main thermal conductivity, tensile stamina, return toughness, and prolongation differ. Select ideal resources according to the efficiency of the target item generated. Amongst the above alloys, A356 has the highest thermal conductivity, and A380 and ADC12 have the most affordable. The tensile restriction is the opposite. A360 has the very best yield toughness and the highest elongation price.
The Alcast Company PDFs
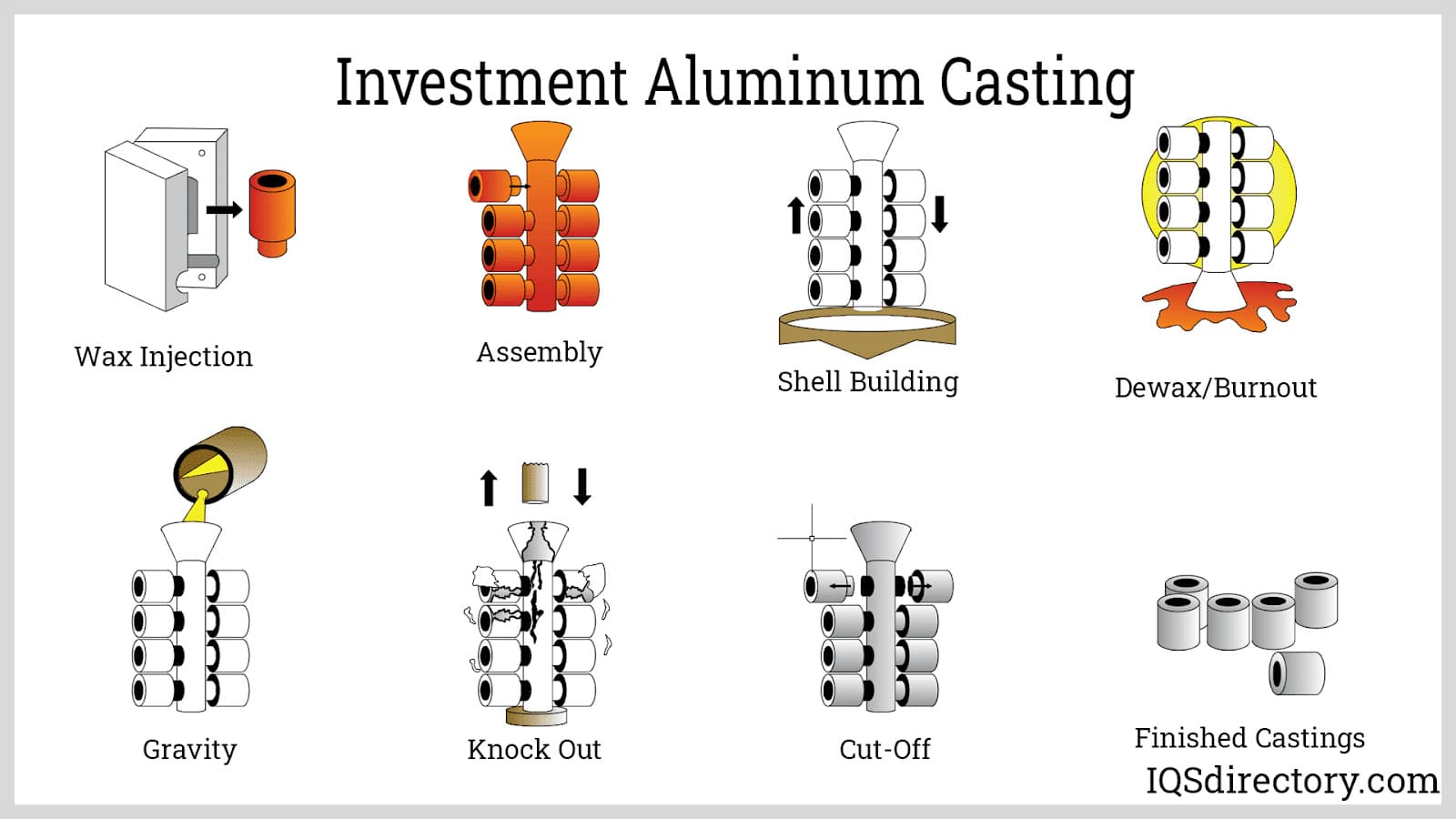
In accuracy spreading, 6063 is well-suited for applications where intricate geometries and top quality surface finishes are paramount. Instances consist of telecommunication rooms, where the alloy's premium formability enables sleek and visually pleasing designs while keeping structural integrity. In the Illumination Solutions market, precision-cast 6063 parts develop classy and reliable lights fixtures that require intricate shapes and excellent thermal efficiency.
The A360 displays remarkable elongation, making it ideal for complicated and thin-walled elements. In accuracy casting applications, A360 is appropriate for sectors such as Consumer Electronic Devices, Telecommunication, and Power Tools.
Not known Incorrect Statements About Alcast Company
Its one-of-a-kind residential properties make A360 an important option for precision casting in these sectors, boosting item longevity and top quality. Light weight aluminum alloy 380, or A380, is a widely utilized casting alloy with numerous unique features. It uses excellent castability, making it a suitable selection for accuracy casting. A380 exhibits great fluidity when molten, ensuring intricate and comprehensive mold and mildews are properly recreated.
In accuracy casting, aluminum 413 beams in the Customer Electronics and Power Tools industries. This alloy's exceptional rust resistance makes it an outstanding option for outdoor applications, making certain resilient, durable items in the pointed out markets.
Alcast Company Fundamentals Explained
Once you have actually chosen that the light weight aluminum die casting procedure redirected here appropriates for your task, a critical following step is picking one of the most proper alloy. The light weight aluminum alloy you pick will significantly affect both the spreading procedure and the buildings of the end product. Due to this, you should make your choice very carefully and take an informed technique.
Identifying one of the most ideal aluminum alloy for your application will certainly imply evaluating a large range of attributes. These comparative alloy features follow the North American Pass Away Casting Association's guidelines, and we've divided them into 2 classifications. The initial classification addresses alloy characteristics that influence the manufacturing process. The 2nd covers features impacting the properties of the end product.
Some Known Details About Alcast Company
The alloy you choose for die spreading straight affects numerous facets of the spreading process, like exactly how simple the alloy is to collaborate with and if it is prone to casting flaws. Hot cracking, also referred to as solidification breaking, is a normal die spreading problem for light weight aluminum alloys that can result in internal or surface-level tears or cracks.
Specific light weight aluminum alloys are much more susceptible to warm fracturing than others, and your option should consider this. Another usual flaw located in the die casting of light weight aluminum is die soldering, which is when the cast stays with the die walls and makes ejection challenging. It can damage both the actors and the die, so you ought to seek alloys with high anti-soldering residential properties.
Deterioration resistance, which is already a noteworthy quality of light weight aluminum, can differ substantially from alloy to alloy and is a vital characteristic to think about depending upon the ecological conditions your product will be exposed to (aluminum casting company). Put on resistance is another residential or commercial property typically looked for in aluminum products and can separate some alloys
Report this page